Mastering Troubleshooting Common Arc Welding Problems
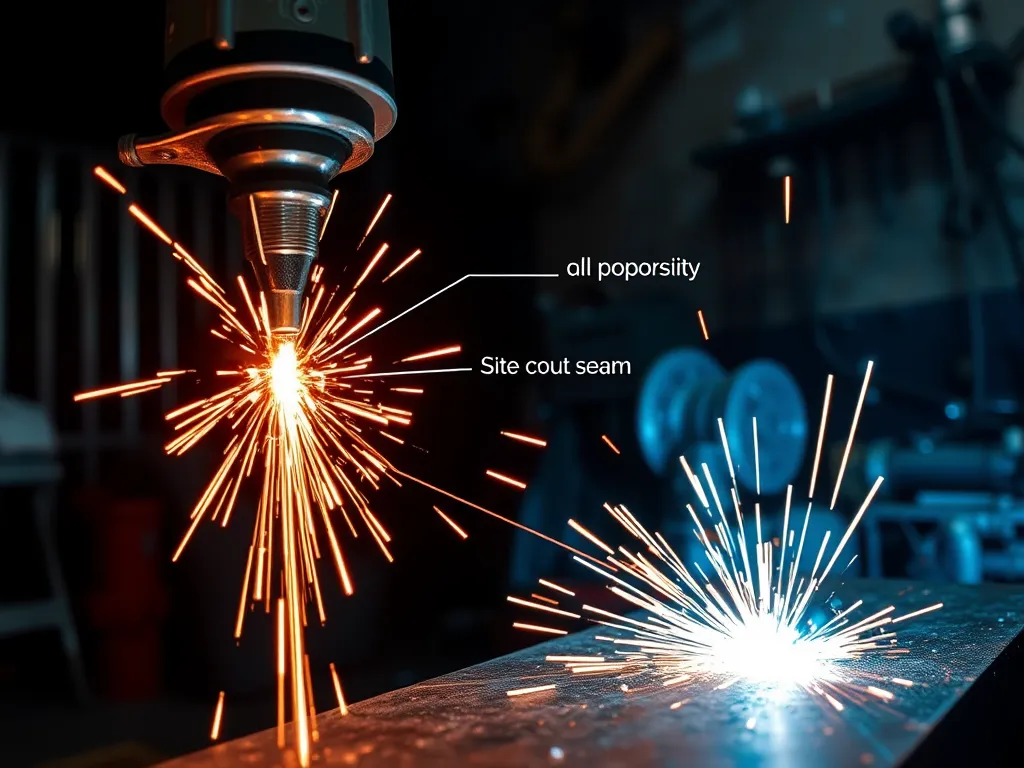
Troubleshooting Common Arc Welding Problems
Arc welding is a commonly used fabrication process that involves creating an electrical arc between a welding electrode and the workpiece to melt the base metals and join them together. However, welders often encounter various problems that can affect the quality and integrity of the welds. In this article, we will discuss effective troubleshooting techniques for common arc welding issues, helping you to navigate and resolve these challenges successfully.
Identifying and troubleshooting common arc welding problems is essential for welders to maintain optimal productivity and ensure the quality of their finished products. Issues such as inconsistent arc stability, material incompatibility, and improper settings can lead to weld defects, making it crucial to understand these problems. This article provides an in-depth look at various aspects of troubleshooting, including equipment issues, material-related challenges, welding techniques, safety concerns, and post-weld inspections that all contribute to effective arc welding processes.
The troubleshooting process begins with understanding the specific issues faced in arc welding. Welders may experience difficulties such as porosity, undercutting, or lack of penetration, all of which can stem from a variety of causes including equipment malfunctions, incorrect settings, or unsuitable materials. By following a systematic approach to troubleshooting, welders can identify the root causes of these issues and implement corrective measures, ensuring a more efficient and effective welding operation.
In addition to technical knowledge, troubleshooting also requires attention to safety considerations and post-weld evaluations. Safety plays a critical role in preventing accidents and injuries associated with welding work, while post-weld inspections are vital for ensuring that the welds meet the required standards and are free from defects. This article will equip you with the necessary insights to successfully address and troubleshoot common arc welding problems, contributing to improved welding performance and enhanced outcomes.
By enhancing your understanding of troubleshooting common arc welding problems, you will be better prepared to handle challenges in the welding shop or field. Focusing on equipment, materials, techniques, and safety measures will lead to higher-quality welds and improved overall efficiency in your projects.
proper voltage adjustments are crucial for achieving optimal weld quality and preventing defects during the welding process.
Welding Equipment Issues
Identifying faulty welding machines is a critical first step in troubleshooting arc welding problems. Common signs of equipment failure include erratic arc behavior, poor amperage control, or an inability to start the arc. Regular maintenance, testing, and inspections of the welding equipment can help prevent these issues. Ensure that your machine is rated for the type of welding you are performing and check for any visible damage or wear on components such as cables, electrodes, and tips.
Maintaining welding cables for optimal performance is also essential for achieving consistent results. Inspect cables for signs of fraying or damage, as these can lead to electrical resistance and reduced arc stability. Ensure that connections are secure and free from corrosion. Properly storing cables by coiling them without kinks will help prolong their lifespan and maintain effective conductivity during welding tasks.
when dealing with electrode issues, identifying the root cause is essential for ensuring a successful welding operation.
Troubleshooting arc stability problems involves examining several factors, such as the welding machine settings, electrode size, and type of shielding gas used. Instability in the arc can produce spatter or uneven weld beads. Adjusting the voltage and amperage, as well as experimenting with different electrodes or gas mixtures, can significantly enhance the stability of the arc, resulting in a more consistent and desirable weld appearance.
understanding effective weld porosity solutions can significantly enhance the integrity and durability of welded joints.
Material-Related Challenges
Selecting the right materials for welding is crucial to ensuring a successful outcome. Different materials exhibit unique characteristics that affect how they respond to heat and welding processes. For example, certain alloys may require specific filler materials or preheating techniques to prevent cracking. Conduct thorough research to understand the properties of the materials you are working with and choose appropriate welding techniques and settings accordingly.
Understanding the impact of material thickness on welding performance is another essential aspect of troubleshooting. Thicker materials generally require higher heat input and sometimes different techniques, such as multiple passes or backstepping, to ensure complete fusion. Conversely, thinner materials are more susceptible to burn-through, necessitating lower heat settings and careful control of travel speed. Assessing material thickness will aid welders in making informed adjustments during the welding process.
Dealing with contamination in welds is a frequent challenge that can lead to defects such as porosity and poor structural integrity. Contaminants like oil, rust, and dirt can inhibit proper fusion between the base metals. Proper cleaning of the work surfaces before welding is necessary to reduce such risks. Implementing methods like wire brushing, grinding, or chemical cleaning ensures that the surfaces are adequately prepared for a strong and reliable weld.
Welding Techniques and Settings
Adjusting the electrode angle for better penetration is a common technique that welders can use to troubleshoot poor-quality welds. The angle of the electrode influences the heat distribution and fusion into the base material. A proper angle, typically between 15 to 30 degrees, can improve the penetration and overall quality of the weld and reduce the chances of defects like lack of fusion or excessive reinforcement.
Understanding voltage and amperage settings is vital for troubleshooting welding problems. Incorrect settings can lead to a variety of issues, including excessive spatter, weak welds, or burn-through. Familiarize yourself with the optimal voltage and amperage parameters for the materials and thicknesses you are welding. Referencing the manufacturer's guidelines can help in fine-tuning these settings for optimal performance.
Common issues with travel speed, such as moving too quickly or too slowly, can adversely affect weld quality. Travel speed impacts heat input and penetration, and inconsistent speed can result in irregular bead appearance and potential voids. Monitoring and adjusting travel speed based on the material and position will enhance the overall quality and consistency of the weld beads.
Safety Concerns in Arc Welding
Identifying hazards during welding processes is crucial for preventing accidents and injuries. Common hazards include exposure to harmful fumes, arc burns, and electrical shock. Conducting a thorough risk assessment prior to starting any welding project can help identify potential hazards and create strategies to mitigate them. Regularly check the work area for potential risks, and ensure proper ventilation to minimize exposure to harmful fumes.
Proper protective equipment (PPE) is essential to mitigate risks associated with arc welding. Welders should wear appropriate PPE, including helmets with suitable filters, gloves, flame-resistant clothing, and safety glasses. Ensuring that all safety gear is in good condition and worn correctly can significantly reduce the risk of accidents and injuries during the welding process.
Emergency response for welding-related injuries is an important aspect of safety planning. Welders should be familiar with the appropriate first aid measures for common injuries, such as burns or electrical shocks. Having a well-stocked first aid kit on-site and knowing the location of the nearest medical facility can expedite treatment in the event of an emergency. Regularly reviewing safety protocols will ensure that all personnel are prepared to respond effectively if a welding-related injury occurs.
Post-Weld Inspection and Testing
Methods for inspecting weld quality include visual inspections and non-destructive testing (NDT) techniques. Visual inspections can help identify surface defects such as cracks, porosity, or undercutting. Employing NDT methods, such as ultrasonic testing or dye penetrant testing, can provide more detailed insight into the internal integrity of the welds without damaging the finished product.
Testing for cracks and other defects is crucial for ensuring welds meet structural requirements. Regularly scheduled inspections and tests can help detect issues before they lead to major failures. Utilizing appropriate testing methods based on the specific application and material will help guarantee the reliability and safety of the welds over time.
Best practices for post-weld treatment involve steps that enhance the durability and performance of the welds. Post-weld cleaning, applying protective coatings, or conducting heat treatment can contribute to improving the corrosion resistance and reducing residual stresses. Implementing these best practices can ensure longer-lasting and more reliable welds, ultimately leading to higher quality outcomes.